AUXILLARY EQUIPMENT
Incineration & Energy SolutionsAir Pollution Control (APC) system, also known as a scrubber or baghouse
The APC system uses air quench cooling, and this takes place in two-stages. The hot gases exiting the secondary combustion chamber meets an ambient air stream (stage 1) and is induced via the by-pass stack. Made of stainless-steel construction, the bypass stack also acts to discharge hot gas, if at any time the ID Fan is stopped. This will automatically occur if the temperature to the bag house exceeds the set maximum temperature and protects the bags from damage by over-temperature.
The 2nd stage air quench is a stainless-steel duct and mixing chamber where air is added under temperature control by a speed controlled blower. This air stream is regulated to maintain the bag house set temperature and must be above the acid dewpoint temperature.
Along with the secondary air quench, powdered lime is added to capture and neutralize acid gases such as hydrogen chloride and sulphur oxides to adsorb very small quantities of the products of incomplete combustion (PICs) such as polyaromatic hydrocarbons (PAHs). The lime feed is mainly recycled from the bag house, with a set, controlled, addition of fresh lime.
Gas flow through the entire plant is maintained by the induced draft fan which is equipped with variable speed control to automatically control draft at the secondary combustion chamber such that fugitive smoke is controlled during loading at the primary chamber.
Energy/Heat Recovery: for the conversion of heat into power
The heat recovery system uses vast amounts of energy, much of which is wasted and enable the efficient and simple conversion of the waste energy into usable electricity which can be used internally to offset electrical costs or sold back to the grid. The system is fully closed which means they have very little chance of being contaminated by the environment, providing long term continuous operation with little maintenance. Each system has an average life cycle of 20 years. Depending on the frequency, temperature and type of incinerator process it is estimated to achieve approx. 25kW to 1MW.
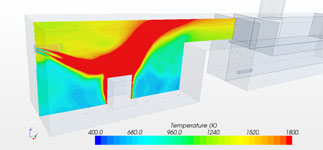
Computational Fluid Dynamics
Computational Fluid Dynamics modelling is used for assurance and proofing of incinerator design. The geometry (physical bounds) of the incinerator is established and the volume occupied by the gas is divided into discrete cells (the mesh) which may or may not be uniform. The boundary conditions are defined which involves specifying the gas behaviour and properties and is then modelled using CFD simulation software resulting in analytical/theoretical data proving incinerator/environmental effectiveness.
Air Pollution Control Monitoring System
Air Pollution Control Monitoring system is a method in which the user can retrieve either live streaming or periodic emission levels of gases exiting the system into the atmosphere. The emission levels can assist the engineer or technician to make on-going adjustments to the incinerator system and ensure greater system efficiency as well as comply to set emission limits.
There are two options available, either online live monitoring or periodic monitoring.
Online Live Monitoring
Continuous emission monitoring can be incorporated into the central HMI PLC control panel to monitor O² and CO², CO gases to ensure the relevant emission standards. The test probes which are built into the stack send data back to the PLC with live readings and record historic data.
Periodic Monitoring
Periodic emission monitoring is a portable flue gas analyser that can be used periodically on the incinerator system. Vacant test ports can be built into the stack and test samples can be retrieved when required. This can read up to 17 different measurement parameters and then can be uploaded to a computer via USB.